Die Hauptvoraussetzung für eine wirtschaftliche Herstellung von Einzelteilen bis hin zur industriellen Fertigung von Elementen aus Holz in hohen Stückzahlen ist der Einsatz von optimalen Hochleistungswerkzeugen. Das Technischen F&E–Zentrum für Oberflächenveredelung und Hochleistungswerkzeugbau in Schömberg-Langenbrand hat ein neues Verfahren zur Oberflächenbeschichtung von Werkzeugschneiden entwickelt und für eine Vielzahl von Werkzeugen und Hölzern bereits in der betrieblichen Praxis erfolgreich eingesetzt.
Ein Hochleistungswerkzeug zeichnet sich durch eine extreme Schneidfähigkeit aus, durch höchstmögliche Abriebresistenz, maximalen Widerstand gegen thermochemische Reduktion und Oxidation, geringe
Neigung zur Benetzung mit Harzen, optimale Spanflächenrauheit,
einen relativ niedrigen Reibungsbeiwert im Kontakt zwischen trockenem Holz und Werkzeugwerkstoff und eine lange Lebensdauer.
Das wichtigste Kriterium für eine optimale Holzbearbeitung ist die Schärfe einer Schneide. Die schärfsten Schneiden erzielt man bei Stahl-Werkzeugen mit einer Härte unter 65 bis 66 HRC (Rockwell-Härte). So scharfe Schneiden wie beim Stahl sind bei Werkzeugen aus Hartmetall, aufgrund seiner gesinterten Struktur, nicht herstellbar. Aus diesem Grund muss der Keilwinkel einer Hartmetallschneide um mindestens 7° größer sein. Das führt in einigen Fällen zu einer unerwünschten Rauheitssteigerung einer gefrästen, einer gehobelten oder einer gedrehten Oberfläche. Noch größer wird der Keilwinkel bei Schneiden aus CBN (Cubisches-Bor-Nitrid) oder dem PKD (Poly-Kristalliner-Diamant) geschliffen. Die Ursache ist ihre dispersive, im Sinterprozess hergestellte, innere Struktur. Mit diesen Werkzeugen hergestellte Holz-Oberflächen haben eine Schruppqualität und müssen einer entsprechenden glättenden Nacharbeit unterzogen werden.
Diese Tatsache zwang bereits in den 1930er-Jahren und zwingt noch heute alle Werkzeughersteller, die ihre Werkzeuge für die Holzbearbeitung bauen, nach neuen leistungssteigernden Werkstoffen für
die Fertigung von stabilen und abriebresistenten sehr scharfen
Werkzeugen zu suchen. Es wurden neue Werkzeugstähle, Schnellarbeitsstähle und Hochleistungsschnellarbeitsstähle für die Bearbeitung von Harthölzern wie Robinie, Eiche, Buche, Douglasie, Ulme,
Eibe und anderen exotischen Hölzern bis zu einer Härte von 270 HB (Brinell-Härte) entwickelt. Bereits in den letzten Kriegsjahren wurden auch gezielt für die Schruppbearbeitung dieser Hölzer
entsprechende Hartmetalle wie z. B. das „K 40“ entwickelt.
In den siebziger Jahren kamen noch pulvermetallurgisch hergestellte Stähle dazu. Die Folge war eine neue Generation von Zerspanungs-Werkzeugen für die Bearbeitung von Hölzern, Metallen, Kunststoffen und verschiedenen hybriden Werkstoffen.
In der gleichen Zeit begann man, sich in der Maschinenbau-Industrie mit der Entwicklung von neuen Hochleistungs-Antrieben und der Erforschung und Herstellung von numerisch gesteuerten Steuerungen für Dreh-, Fräs- und Schleifmaschinen mit sehr großem Erfolg zu beschäftigen. Die Drehzahl und die Leistung der Antriebe konnte beträchtlich erhöht werden. Daraus entstanden die heutigen bis zu fünf-achsigen, sehr genauen CNC-Bearbeitungszentren mit geregelten Spindel-Drehzahlen von 1000 bis über 30 000 U/min.
Industrielle Beschichtungsverfahren für Werkzeugoberfläche
Leider ist seit der letzten Werkzeug-Werkstoff-Entwicklung bis 1980 praktisch nichts Nennenswertes auf diesem Gebiet passiert. Sehr viel passiert ist aber im Zeitraum von 1955 bis 1980 in der Werkzeug-Oberflächenveredelung: Es wurden verschiedene neue Verfahren entwickelt und industrialisiert, so das Hochtemperatur-CVD-Verfahren (chemische Abscheidung aus der Gasphase, engl. Chemical Vapor Deposition) und drei PVD-Verfahren (Physical Vapor Deposition): Das Abscheiden von Hartstoffen mittels Elektronen- Strahlkanone, auch als Balzers-Verfahren bekannt, das Abscheiden von neuen Werkstoffen mithilfe einer Wolfram- Elektrode, auch Multi-Arc-Verfahren genannt, und zuletzt die Herstellung von Hartstoffen mittels Zerstäubungs- Verfahren von hochschmelzenden Metallen.
Mittels aller drei PVD-Verfahren werden Hartstoffe reaktiv in Form von Metall-Nitriden, -Karbonitriden und -Oxiden auf einer entsprechenden Werkzeugoberfläche in einer Stärke von 4 μm bis 10 μm abgeschieden (1 μm = 0,001 mm). Eine Abscheidung von Metall-Karbiden ist aus physikalischen Gründen praktisch nicht möglich. Leider gibt es bis heute auch aus physikalischen Gründen mit der direkten Haftung der abgeschiedenen Hartstoffe an der Werkzeugoberfläche Probleme. Schwierigkeiten bereitet auch die unerwünschte Oberflächenrauheit (Mikro-Alpen-Struktur). Ein Hindernis bei der Herstellung von Hartstoff-Schichten mit Dicken unter 4,5 μm sind Nano und Mikrokapillaren. Sie erstrecken sich von der Schichtoberfläche bis zum Substrat und sie wachsen erst oberhalb einer Schichtdicke von 4,5 μm zu. Ein weiteres Problem ist die Herstellung einer gleichmäßigen Schichtdicke an den Kanten und Funktionsecken einer Schneide.
In der Industrie wird die Haftfestigkeit dieser Schichten mittels eines Kratztests festgestellt. Sie liegt zwischen etwa 60 N und 70 N. Um den Wert zu verbessern, bedient man sich zweier Methoden: Die erste beruht auf der Abscheidung einer relativ weichen dünnen Zwischenschicht. Mittels der zweiten wird die Werkzeugoberfläche im Mikrobereich „gezielt“ aufgeraut. Leider liegt die Haftung der Hartstoffe nach der Anwendung beider Methoden noch immer weit unter der gewünschten Grenze von 100 N und wird dennoch in vielen Anwendungsfällen als ausreichend definiert. Dieser Umstand motiviert viele Forscher, noch weiter an der Steigerung der Haftfestigkeit, der für viele Anwendungen mittels PVD-Technologien hergestellten Me-Nitride, Me-Karbonitride und anderer Metalle intensiv zu arbeiten.
Für die Bearbeitung von Weich und Harthölzern, MDF, Spanplatten, Kunststoffen, GFK, sowohl Weich- als auch Hart-Gummi und Nichteisen-Metallen sollte der Schneiden-Radius eines Zerspanungswerkzeugs wenn möglich zwischen 0,01 mm und 0,005 mm liegen. Somit sollte sich nach einer Oberflächenveredelung der Radius um nicht mehr als 0,002 mm vergrößern. Passiert das, so stellt das bereits das erste Verstumpfen einer Schneide dar. Die direkte Folge im Zerspanungsprozess ist eine zusätzliche Reibungswärme-Entwicklung an der Schneidkante, was zu einem entsprechenden Festigkeitsverlust im Schneidkeil-Werkstoff führt. Dieser Verlust ist die Ursache für eine beschleunigte Abnutzung der Schneidkannten, der Span- und der Freiflächen. Die Folge dieser Veränderung ist eine proportionale Verschlechterung der Rauheit von gedrehten, gefrästen, gehobelten oder gesägten Holz-Oberflächen.
Erreicht der Verschleiß der Schneide einen Grenzwert, so steigt die Reibung zwischen der Werkzeugschneide und der Holzoberfläche so stark an, dass sich das Holz zu verfärben und anschließend zu brennen beginnt. Eine weitere Ursache für eine Temperatursteigerung in einem Werkzeug und damit eines gesteigerten Festigkeitsverlustes ist eine nicht optimale Oberflächenrauheit der Schneidkante und ihrer Funktionsflächen.
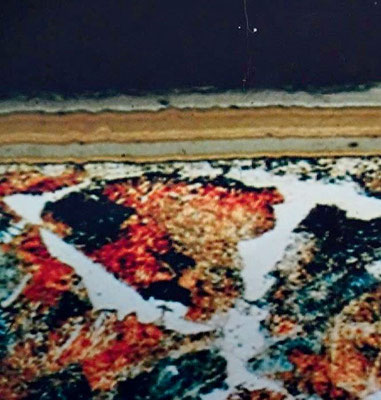

(Abbildung 1. & 2.)
Multielementige karbidische Nano-Hartstoffschichten (jeweils grau) in unterschiedlicher Vergrößerung, Schichtdicke 1,7 µm, Mikrohärte 3000 - 3200 HV
Neues Tieftemperaturverfahren reduziert Verschleiß
Mit dem Verstumpfen der Schneiden im Holz beschäftigt sich das Technische F&E-Zentrum für Oberflächenveredelung in Schömberg seit 1998. Man hat hier Werkzeuge aus Kalt-, Warmarbeits und Schnellarbeits-Stahl, aus Hartmetall und CBN sowohl bei nicht beschichteten als auch bei mit PVD- und 3D-Tieftemperatur-CVD-Verfahren (3D-TT-CVD) beschichteten Bohrern, Fräsern und Hobelmessern in verschiedenen Holzarten untersucht. Die besten Ergebnisse erzielte man mit multielementigen karbidischen Hartstoffen in einer Schichtdicke zwischen 1,5 μm und 2 μm und einer Mikrohärte zwischen 3 100 und 3 200 HV (Vickers-Härte; Abbildung 1 und 2).
Das neue 3D-TT-CVD-Verfahren ist ein hochenergetischer Oberflächenveredelungsprozess. Dieser Prozesstyp ermöglicht eine definierte, dynamische Beeinflussung aller chemischen und physikalischen Eigenschaften während des Herstellungsprozesses einer karbidischen, nitridischen, oxidischen oder einer entsprechenden multielementigen Super-Hartstoffschicht. Hierbei handelt es sich um ein Vakuumverfahren. Hier kann die Konzentration aller im Beschichtungsprozess teilnehmender Elemente in jedem genannten Super- Hartstoff beliebig von 0 % bis 100 % variiert werden. In einigen Fällen reicht bereits eine Zugabe im Mikrogramm-Bereich von einem oder mehreren metallischen Elementen zur Legierung des Hartstoffs auf einer Werkzeugschneide, um eine besonders hohe Standzeit zu erzielen. Die Schichtdicke von Hartstoffschichten für Werkzeuge, die für die Holzbearbeitung bestimmt sind, liegt im Bereich zwischen 1,5 μm und 2,1 μm.
Mittels dieser Methode können sowohl massive als auch aus unterschiedlichen Werkstoffen zusammengesetzte Werkzeuge, im Temperaturbereich zwischen 480 °C und 600 °C, mit binären oder multielementigen Super-Hartstoffen beschichtet werden. Mit dieser Methode ist es gelungen, die optimal hergestellte Schneiden schärfe sehr stark und relativ lange zu stabilisieren. Die entsprechende Zusammensetzung der dünnen Schicht reduzierte die Neigung der Hartstoffoberfläche zum Verkleben, verursacht von mit Harzen gesättigten Holzspänen. Die hohe Mikrohärte der Superschichten von etwa 3 000 HV bis 3 200 HV hat einen gravierenden Einfluss auf die Steigerung der Abriebresistenz der Werkzeugschneide. Wenn man bedenkt, dass der Härte eines auf 63 HRC gehärteten Werkzeugs nur eine Mikrohärte von 740 HV entspricht, so ist es klar, dass sich der Abriebverschleiß viermal langsamer entwickeln müsste.
(Abbildung 3. & 4.)
Mit (FeCrMeVTi)-C im 3D-TT-CVD-Verfahren beschichtete HSS-Hobelmesser, Oberflächenhärte 3000 - 3200 HV. Im vergleich zu nicht beschichteten Schneiden erhöht sich die Standzeit um rund 700%.
Werkzeugstandzeiten um Faktor 5 bis 18 verlängert
Vor zweieinhalb Jahren wurde dieses Verfahren vollständig industrialisiert. Seit diesem Zeitpunkt wurden unterschiedliche Werkzeuge entsprechend veredelt und in der Holzbearbeitung eingesetzt. Zu unserer Überraschung wurden wir hier mit sehr hohen Standzeit-Steigerungen konfrontiert. Und so konnten Werkzeuge dank der Oberflächenveredelung mit multielementigen Hartstoffen entsprechende Verbesserungen bei zahlreichen Holzarten erzielen. Dank der Beschichtung von Dübelbohrern (D12/B30/L55,5/S8x20) aus Schnellarbeitsstahl mit dem Hartstoff HSS7000.A-(FeCrVWTi)C konnte die gesamte Lebensdauer dieser Werkzeuge um den Faktor 5 bis 18 – je nach Härte der zu bearbeiteten Holzart und ihrer Feuchtigkeit – im Vergleich zu mittels PVD-Technik mit TiCN beschichteten Bohrern weiter verbessert werden.
Genauso gute Ergebnisse erreichte man dank der Oberflächenbeschichtung bei Forstner-Bohrern in Pockholz (88 HB; Standzeitsteigerung: Faktor 9 bis 12), bei Langloch-Bohrern in Ahorn (27 HB; Standzeitsteigerung: Faktor 8 bis 10), Schlangen-Bohrern in Douglasie (20 HB; Standzeitsteigerung: Faktor 6 bis 9), Holzspiralbohrern in Kiefer (19 HB, Standzeitsteigerung: Faktor 8 bis 16) und Zapfenschneidern in Birke (23 HB; Standzeitsteigerung: Faktor 7 bis 11).
Ähnlich gute Resultate wurden bei mittels multielementigen karbidischen Nano-Hartstoffschichten veredelten Werkzeugen wie Vollhartmetall (VHM)-Doppel-Karnies-Profilfräsern in Eichenholz (Standzeitsteigerung: Faktor 9 bis 15), VHM-Gratfräsern (Zinkenfräser) in Buchenholz (34 HB; Standzeitsteigerung: Faktor 8 bis 14), VHM-Spiralnutenfräsern rechts und links in Buche (Standzeitsteigerung: Faktor 9 bis 11), VHM-Gratleistenfräsern in Robinie (48 HB; Standzeitsteigerung: Faktor 6 bis 11), VHM-Halbkehlfräsern, Nutenprofil- und Multiprofilfräsern in Weiß-Eiche (34 HB; Standzeitsteigerung: Faktor 10 bis 16), Scheiben-, Zinkenfräsern, HSS- und VHM Wendeplatten in Ulme (30 HB; Standzeitsteigerung: Faktor 6 bis 11), HSS Furniermessern in Birke (23 HB; Standzeitsteigerung: Faktor 6 bis 9), HSS Streifenhobelmessern (1200, 1050, 800, 600 x 35 x 3 oder L x 12 x 2) in Kiefer (19 HB; Standzeitsteigerung: Faktor 5 bis 10), erzielt (Abbildung 3 und 4).
Die praktische Anwendung dieses Verfahrens in der Oberflächenveredelung von sowohl neuen als auch in Stand gesetzten Bohrern, Fräsern, Hobelmessern, Schneidmessern und Wendeschneidplatten führt zu einer proportionalen Senkung bei der primär geplanten gesamten Werkzeuganzahl sowie bei zahlreichen, die Werkzeuge betreffenden Kosten wie die für Beschaffung, Eingangskontrolle, Voreinstellung und Nachschleifen.
Die Perioden zwischen einzelnen Werkzeug-Instandsetzungen verlängern sich, die Anzahl der Umrüstperioden und die Maschinenstillstandszeiten dagegen verringern sich, genauso wie die Kosten für Werkzeug-Lagerflächen und Energie. Die Stromaufnahme bei der Zerspanung mit Werkzeugen, die mit einer Super-Hartstoffschicht beschichtet sind, ist durchschnittlich um 12 % bis 18 % reduziert.
Seit geraumer Zeit werden im Technischen F&E-Zentrum Werkzeuge für holzbearbeitende Betriebe hergestellt, abgenutzte Werkzeuge mittels qualifizierten, den Werkzeug-Werkstoff schonenden Methoden instand gesetzt und mit entsprechenden binären oder multielementigen Nano-Hartstoffschichten veredelt.
Dieser Artikel erschien im Holz-Zentralblatt Nr. 47 vom 23. November 2018
Autoren: Dr.-Ing. Lienhard J. Paterok, Dipl.-Ing. Leonhard F. Paterok, Dipl.-Ing. Peter Sigmond, Guido Jänicke.